Understanding What is Porosity in Welding: Reasons and Solutions
Understanding What is Porosity in Welding: Reasons and Solutions
Blog Article
Understanding Porosity in Welding: Exploring Causes, Effects, and Prevention Methods
Porosity in welding is a persistent obstacle that can dramatically affect the high quality and integrity of welds. As professionals in the welding market are cognizant, recognizing the causes, results, and avoidance techniques connected to porosity is important for attaining robust and dependable welds. By delving into the root causes of porosity, examining its harmful results on weld high quality, and discovering effective prevention strategies, welders can boost their understanding and abilities to produce premium welds regularly. The detailed interaction of aspects contributing to porosity requires a thorough understanding and a proactive strategy to make sure effective welding outcomes.
Typical Reasons For Porosity
Porosity in welding is largely triggered by a combination of variables such as contamination, inappropriate shielding, and inadequate gas coverage throughout the welding procedure. Contamination, in the kind of dust, grease, or corrosion on the welding surface, develops gas pockets when heated, leading to porosity in the weld. Improper protecting happens when the protecting gas, generally made use of in procedures like MIG and TIG welding, is unable to fully safeguard the liquified weld pool from reacting with the surrounding air, causing gas entrapment and succeeding porosity. In addition, inadequate gas insurance coverage, typically as a result of wrong flow prices or nozzle positioning, can leave components of the weld vulnerable, allowing porosity to develop. These variables jointly add to the formation of spaces within the weld, deteriorating its honesty and possibly creating architectural issues. Comprehending and resolving these typical reasons are critical steps in preventing porosity and making sure the top quality and stamina of welded joints.
Effects on Weld High Quality
The presence of porosity in a weld can considerably compromise the total quality and honesty of the welded joint. Porosity within a weld creates gaps or tooth cavities that weaken the framework, making it much more prone to splitting, corrosion, and mechanical failing. These spaces work as stress and anxiety concentrators, minimizing the load-bearing capability of the weld and enhancing the likelihood of early failure under used anxiety. Additionally, porosity can additionally act as possible websites for hydrogen entrapment, more intensifying the deterioration of the weld's mechanical residential properties.
In addition, porosity can prevent the efficiency of non-destructive testing (NDT) methods, making it testing to spot various other problems or gaps within the weld. This can result in substantial safety and security issues, particularly in important applications where the architectural integrity of the welded parts is critical.

Avoidance Techniques Review
Offered the destructive influence of porosity on weld quality, reliable avoidance methods are vital to preserving the structural honesty of welded joints. In addition, choosing the proper welding criteria, such as voltage, existing, and take a trip speed, can help minimize the risk of porosity development. By incorporating these prevention strategies right into welding techniques, the incident of porosity can be considerably minimized, leading to more powerful and much more reliable bonded joints.
Relevance of Proper Shielding
Correct protecting in welding plays an important role in protecting against atmospheric contamination and making sure the stability of welded joints. Shielding gases, such as argon, helium, or a mix of both, are typically used to shield the weld pool from responding with aspects in the air like oxygen and nitrogen. When these reactive aspects enter call with the warm weld swimming pool, they can create porosity, leading to weak welds with decreased mechanical buildings.
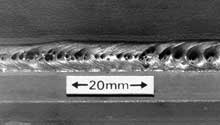
Inadequate securing can result in various defects like porosity, spatter, and oxidation, endangering the architectural integrity of the bonded joint. Therefore, sticking to correct securing methods is vital to produce top notch welds with minimal flaws and make sure the long life and reliability of the welded components (What is Porosity).
Surveillance and Control Methods
Just how can welders efficiently check and regulate the welding process to guarantee optimum outcomes and stop defects Check Out Your URL like porosity? One secret method is through using advanced tracking modern technologies. These can include real-time tracking systems that provide comments on specifications such as voltage, existing, take a trip rate, and gas flow rates. By continuously keeping find here track of these variables, welders can determine discrepancies from the perfect problems and make instant modifications to avoid porosity formation.

In addition, executing proper training programs for welders is necessary for keeping an eye on and controlling the welding process effectively. What is Porosity. Informing welders on the value of preserving regular criteria, such as proper gas protecting and travel speed, can help prevent porosity issues. Routine evaluations and accreditations can additionally make sure that welders are skilled in monitoring and controlling welding procedures
In addition, making use of automated welding systems can enhance surveillance and control capabilities. These systems can exactly manage welding parameters, reducing the possibility of human mistake and making certain consistent weld quality. By incorporating innovative monitoring innovations, training programs, and automated systems, welders can efficiently keep track of and manage the welding process to lessen porosity click resources issues and attain top notch welds.
Final Thought
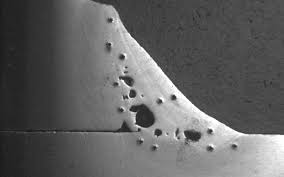
Report this page